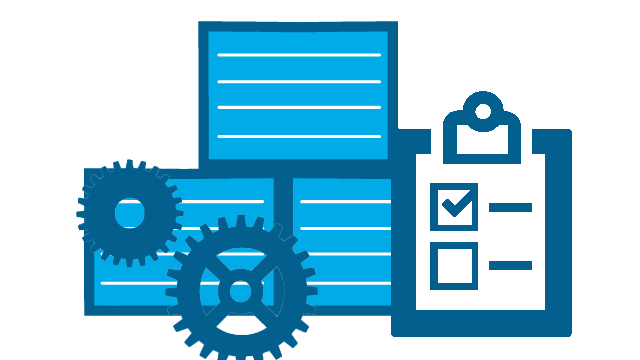
Las diferencias de inventario juegan un papel importante en las empresas, no solo porque tienen un impacto económico que en la mayoría de las ocasiones se transforma en pérdidas, sino además porque es un indicador operacional de la eficiencia logística y el cumplimiento o no de una estrategia ‘Lean’ en la empresa.
El control de stock es clave en la cadena de suministro. El stock condiciona diferentes áreas tales como: producción, compras y ventas. La estrategia de stock deberá estar alineada a estos tres departamentos y a otros que pueda influir, en caso contrario probablemente los objetivos de diferencias de stock no se verán cumplidos.
Existe una diferencia entre gestión de stocks y optimización de stocks. Gestión de stocks es básicamente el software que registra todos los movimientos, por ejemplo el SAP. Por otro lado, optimización de stocks refiere al nivel adecuado en unidades y tiempo en que la planta productiva lo necesita para evitar parar la producción. La optimización de stocks conlleva unos costes de almacenamiento y gestión de flujos internos en la cadena de suministro.
A menudo tendemos a generalizar procesos en cuanto a gestión de stocks y hay que diferenciar de qué sector y producto se trata. Se habla cada vez más de la tecnología RFID como la mejor herramienta para la gestión del stock. Pero aunque se invierta en el desarrollo de una tecnología parecida al RFID para controlar el inventario, ésta se enfrenta a dos grandes hándicaps. En primer lugar, tanto las empresas proveedoras como los clientes deberían utilizar un software igual o similar para poder volcar datos informáticos y no perder la trazabilidad de los componentes.
En segundo lugar, no es lo mismo controlar un producto acabado que entra y sale de almacenes y tiendas frente a un componente que experimenta transformaciones en máquinas o “inventario vivo”. La mayoría de las plantas productivas hacen inventario 1 o máximo 2 veces al año por las características que presenta el “Inventario vivo”. En estos casos, hay que parar la fábrica y asegurarse de que nadie esté trabajando para poder hacer un recuento de los componentes, tanto de los que están dentro cómo de los que están fuera de la máquina, más todos los que están almacenados. ¿Podemos mejorar este sistema tradicional con la Industria 4.0? ¿Cuándo?
La complejidad de gestionar todos los puntos que interfieren en un “Inventario vivo” implica más personal. Mientras tanto, y adoptando el rol de “Demand Planner”, para evitar una parada de la producción por falta de stock por causa de un descuadre, algunas buenas prácticas serían las siguientes:
1. Fijar stocks mínimos en almacén. Habrá más flexibilidad en función de si el almacén es de consigna o propio.
2. Revisar los consumos de los componentes mínimo una vez al mes, ya que la demanda no es estable y la composición de fabricación no siempre es la misma.
3. Asegurar que los datos maestros de cada componente (SKU) sean correctos, sino el MRP (Material Replenishment Planning) no se recalculará bien.
4. Analizar el servicio de los proveedores y poner especial atención en aquéllos que siempre sirven con retraso o con problemas de calidad.
5. Revisar el stock y comprobar los pedidos, máximo cada dos días.
6. Si existe alguna herramienta para detectar descuadres diarios, solucionarlos. Así evitamos llegar a finales de año con diferencias de stock acumuladas y difíciles de solucionarlas.
7. Cuando un producto ha cambiado alguna referencia, poner especial atención al cambio de éste, no sólo al que dejaremos de consumir sino también a la introducción del nuevo.
8. Hacer controles puntuales de algún “SKU” en planta para asegurar que el stock es correcto.
18-04-2018 / GS1 Perú